The future of rare earth recycling
Companies are scrambling to find ways to reuse costly rare earth elements
Kathryn Free • March 3, 2014
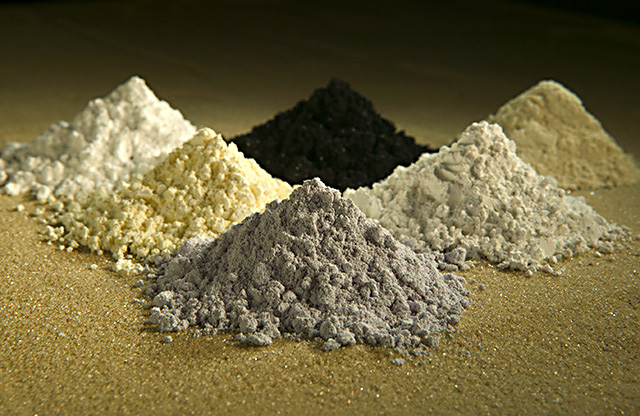
Rare earth elements like these are used in a wide variety of technologies, from magnetic resonance imaging to fluorescent lighting. Clockwise from top left: gadolinium, praseodymium, cerium, lanthanum, neodymium and samarium. [Image credit: Wikimedia Commons]
What do a smartphone, a hybrid car and a Tomahawk cruise missile have in common? They won’t work without obscure rare earth elements. Scarce materials like europium, neodymium and others are now so in demand that companies and governments are urgently considering unlikely places to mine them, including deep under the sea and, someday, even asteroids.
But there’s another option that has been getting a lot of attention lately: recycling. While there are many challenges ahead, some experts think that recycled rare earths from scrap materials and discarded products may eventually be able to meet up to 40 percent of global demand. That could be a boon for the U.S. and other Western nations, since China now dominates the world market for rare earths and can effectively control their supply and price.
The thing about rare earths is that they aren’t especially rare. Even the two scarcest, thulium and lutetium, are almost 200 times more abundant than gold. Yet the rare earths are difficult to mine because they’re spread out within the Earth’s crust.
“Rare earths are the pepper and salt in many new technological applications,” says Koen Binnemans, a rare earth scientist at the University of Leuven in Belgium. “There are a few applications where no other elements can do the job.”
These metals are valuable because they each have distinctive — and rare — qualities. Neodymium and samarium, for example, are strong magnets, making them crucial for computer hard drives and headphones. Cerium is a powerful catalyst used as an additive to diesel fuel. Europium and terbium are needed for fluorescent light bulbs.
As the demand for rare earths has risen, countries have scrambled to get their share. Right now, China exports more than 80 percent of the world’s supply.
But as people in China move up the economic ladder, they and their families want the same kinds of consumer devices that we have, says Jim Sims, a representative of Molycorp, the only company in the U.S. that mines rare earths. “That alone is driving increased demand.” In July 2010, China decreased its rare earth exports by 70 percent and prices soared. Costs have stabilized since then, but rattled nations are urgently looking beyond China for the valuable metals.
“People in [Washington] D.C. for sure at some point woke up and said, ‘Gee, we like magnets and fluorescent lights and batteries and oh boy, all of this stuff we need is coming from China. We better do something about it,’” says Corby Anderson, who teaches metals mining and engineering at the Colorado School of Mines. As a result, the U.S. Department of Energy announced last year that it was starting the Critical Materials Institute at the Ames Laboratory in Iowa to tackle the issue.
In 2010, Molycorp reopened its rare earth mine in Mountain Pass, Calif., which had closed down in 2002. Other mining companies, meanwhile, are looking for potential new mine sites around the world. Some of those sites may even be several miles underwater, near hydrothermal vents at the bottom of the ocean — an idea several companies are seriously considering. An even more far-out idea is to explore the moon and asteroids for rare resources. Companies like Planetary Resources are already raising money and someday hope to mine the skies.
While these unconventional ideas are getting most of the attention, some researchers are focusing on less flashy but likely more practical ways of procuring rare earths: by recycling the metals from scrap and thrown-away products such as used cell phones and fluorescent bulbs. Despite all the recycling research now underway, less than one percent of all rare earths were recycled in 2011. Scientists haven’t yet figured out how to efficiently recapture the elements.
“Recycling is in its infancy,” says Colorado’s Anderson. “Sometimes the challenges you face are more formidable than primary production.”
Breaking down highly engineered products like cell phones requires extra labor and extra chemical steps to isolate the rare earths, adding to the cost. And each technology requires a different recycling technique — what separates terbium from light bulbs won’t isolate neodymium from a hard disk drive.
Another consideration is that rare earths aren’t the only materials worth recapturing. “You have to develop special methods for each application so not only do you recycle the rare earths but the other valuable metals that are present,” says Belgium’s Binnemans. “Too often, people from academic research are too focused on getting just rare earths back, but that is the wrong approach.” One of the reasons why rare earth recycling is only now starting is that past efforts focused on recovering expensive metals like gold and copper and ignored the once cheaper rare earths.
For now, the most promising recycling process may be obtaining rare earths from fluorescent light bulbs. In Europe, consumers are required to recycle bulbs because they contain mercury, so recycling companies have immediate access to the materials. Solvay, a chemical and plastics company based in Belgium, has already begun to extract six separate rare earth elements from fluorescent bulbs and has recycled more than 1,000 tons of product, according to Frederic Carencotte, who heads the rare earth division at Solvay. To recycle the bulbs, workers at Solvay separate the rare earths from everything else. Next, they isolate each one and recombine them to make a fluorescent precursor that they sell back to lamp manufacturers.
Other companies are looking beyond bulbs in their quest for recycled material. Around 20–30 percent of rare earths used in magnet production end up as scrap waste, so companies are beginning to collect the scrap to reuse it. In addition, a Chinese research team recently used nanoparticles to capture more than 85 percent of the rare earths from wastewater. But Colorado School of Mines’ Anderson suggests the Chinese results aren’t a breakthrough: the hard part is to separate rare earths from each other, not merely to capture them.
Since hybrid cars require rare earths in their batteries, companies such as Honda and Toyota are working hard to recycle them and cut battery prices. Recycling “could be the winning weapon to excel in the global car market,” says Marcello Ruberti, a rare earths economist at the University of Salento in Italy. Separating rare earths from cell phones, on the other hand, is more difficult and costly because the parts are so small that it requires a lot of labor to take the phones apart.
In the long run, recycling may not only prove to be an economic boon, but also a plus for public health and the environment. Rare earth ores almost always include a small amount of radioactive material, such as uranium and thorium. In 2004, researchers published the results of a 20-year study on workers from the Baiyun Obo Mine in China. They found that thorium exposure over a long period of time caused a higher incidence of lung cancer. With recycling, however, the radioactive materials would already be removed when workers handle the metals.
Binnemans, the Belgian researcher, thinks companies could recycle more than 40 percent of the rare earths in fluorescent lights. Other products, such as car batteries and industrial scrap, could follow if recycling technologies continue to improve. But it’s unlikely that the world’s ever-increasing hunger for rare earth metals could ever be fully satisfied with recycled material. “I think it’s unrealistic to think that 80 to 90 percent of rare earths will be recycled. But I would be happy if we could have an average of recycling more than 10 percent,” says Binnemans.
“That would be a huge progress compared to what we have at this moment.”